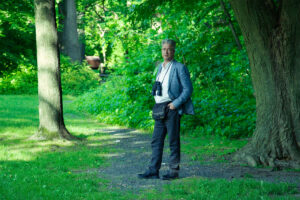
Steven Peck – Green Roofs for Healthy Cities
Steven Peck is dedicated to creating greener, healthier & resilient cities with nature & urban agriculture.
USA
IA YIEN LEI December 28, 2022
Michelle Kaufmann, the Director of R+D Lab for the Built Environment at Google, is a leading architect known for her passion for thoughtful and accessible designs and sustainable, humane, technology-wired architecture. Kaufmann believes that sustainable design and architecture reduce negative impacts on the environment and supports the health and comfort of building occupants.
Kaufmann founded Michelle Kaufmann Designs in 2002, where she successfully designed and built innovative single-family and multi-family green homes using prefabricated modular technology. As a result of the housing crisis in 2009, she closed her business. She joined Google after meeting Astro Teller and Sebastian Thrun, who had recently co-founded Google X with Sergey Brin. With their interest in solving the problem of affordable, healthy, durable housing, Kaufmann was invited to join their team. During that time, Kaufmann also co-founded the start-up company, Flux, to work on the problem of scalable, affordable buildings. Flux later became part of Google’s Alphabet.
As the director of the R+D Lab for the Built Environment at Google, the work Kaufman is leading has the potential to positively impact millions of lives.
Mood of Living: Where did you grow up?
Michelle Kaufmann: I grew up in Iowa, near farmlands, where the sky is big and everyone greets each other in terms of the weather and what the land needs (“Morning! Farmers sure could use some rain…” or “Hi. Good we have rain today – the crops sure needed it.”). I was greatly influenced by the original environmentalist entrepreneur: the farmer, who is always in tune with the environment and solves problems as they arise with scrappiness, hard work and tenacity.
MoL: What or who inspired your interest in architecture and sustainability?
MK: My parents and family really inspired me. I come from a long line of hard-working problem solvers, many of whom are farmers and/or factory workers. If you need something, you make it yourself out of whatever you have around in the garage, the workshop, or the storage shed. My dad’s hobby was flying airplanes, so he built one in our garage. I grew up with an airplane parked in our driveway and our cars parked on the street. When you grow up with that kind of mindset, you develop a deep-rooted appreciation for the environment and an unshakable life goal of getting more out of less.
Childhood family home
MoL: What did you study at Iowa State University? Did your studies influence your professional direction?
MK: I studied at Iowa State where I received my undergraduate Bachelor of Architecture degree. For decades ISU has been a highly respected Architecture program that prioritizes teaching the fundamentals of becoming a trusted practicing architect who knows how to solidly put together functional and thoughtful buildings. ISU plus my internships at RDG set an incredible foundation for my journey in design and architecture.
MoL: What or who influenced your decision to get your master’s degree in architecture from Princeton University? What was your focus at Princeton? Was sustainable design integral to your studies?
MK: While at ISU, I was very fortunate to study under Jennifer Bloomer who is an extraordinary architect, thinker, writer and theorist. She empowers her students to be highly inclusive and to embrace and empower positive human experience for all – not just the kind of iconic BIG A architecture of landmarks but for the everyday. She is the one who inspired and supported me to go to Princeton as a continuation of my education. At Princeton, I was lucky to be able to study under Liz Diller of Diller Scofidio. She is a legend. Her work and thinking are smart, brave and fresh. She helped me learn to not be held back by conventional practices or approaches, but instead look at design without boundaries.
Michelle Kaufman
MoL: You worked for Frank Gehry after Princeton. What was this experience like? What were the most important takeaways from working at this firm?
MK: Yes, it was my first job after graduate school, and I loved it! It was an incredible education on the power of place and the positive impact great design can have on people – watching people weeping when they visited Bilbao Guggenheim for the first time. It was there that I learned how to make highly ambitious curved shapes in constructible ways. One role I played was helping to bring in a software called Rhino, since Catia wasn’t scalable at the time, and Gehry Technologies hadn’t been commercialized yet. Only four or five of us out of a hundred people were using Catia at the time, so we brought in Rhino to help. The digital aspect of bringing together design plus build is actually a connected thread of my career, even though it was never what I set out to do. I never thought of myself as a digital person, but that has turned out to be a key type of glue for me in thinking about ways to make sustainable design accessible to all.
Santa Barbara Modular House
MoL: What inspired you to start your own business as a pioneer in green architectural design, and in creating prefab houses? What were the challenges of creating and owning your own architectural firm?
MK: It started when my husband Kevin and I were looking for a home to buy and, when it became clear we weren’t able to find anything that we liked that we could afford, we decided to design and build for ourselves. especially in California. So much of what we saw was poorly designed. It’s a significant problem in the United States – that most homes are not healthy or efficient or with timeless beauty. After we built our house in northern California, we had several friends who asked if the couple could build similar homes for them. Thus, our MKD (Michelle Kaufmann Designs) company was born! Having determined we wanted to embrace a modular building method to minimize costs and waste, we went on to replicate our own home using prefabricated modular systems with sustainable healthy materials.
Modular homes produce about 50 to 75 percent less waste than site-built ones, which average about 7,000 pounds of waste. Few people would build a car on their driveway, so why build a house from scratch on-site? As the MKD business grew, it became apparent that being able to control the whole process, from manufacturing through completion, was essential. At MKD we hit walls trying to innovate with new approaches or alternative materials. Most of the factories we talked to had the same mindset based on high margins and low volume. They weren’t interested in discussing creating some crazy new countertop made of recycled paper. So, we took what seemed the obvious step and bought a factory. It was in Seattle, which was close to several other companies they did business with, including a window supplier and a factory that provided us with Forest Stewardship Council-certified wood. That changed the game for us as it opened up the ability to design the elements we wanted and to grow.
Northern Ca House
MoL: Can you explain what prefabricated modular technology is? Why are prefab homes considered sustainable?
MK: A modular home is constructed using three-dimensional boxes or “modules”. The home is built to site-built code but created in a factory. Interior and exterior sheathing, utility lines, interior partitions and stairs are all completed in the factory. The modules are 90-95% complete when they come off the assembly line in the factory. After completion in the factory, a modular home is shipped to the site, then attached to a permanent foundation at the building site. Several modules can be connected side-by-side or stacked to create a finished home. When completed, modular homes are composed of several modules fastened together. Once the home is attached, it is considered real estate and appraised against other custom site-built homes.
The Benefits of Modular homes:
Not all factory-built homes are on a level playing field. Among the many classifications of prefabricated homes are modular homes, manufactured homes, and mobile homes. Each of these home types is very different. Although they are all built in a factory, they are built to different building codes, with modular construction at the highest construction/quality level. Many city and county zoning ordinances restrict the locating of manufactured/mobile homes to limited areas, whereas modular homes are more widely accepted.
Smart Home Chicago
MoL: What led you to Google? What expertise did you bring?
MK: I met Astro Teller and Sebastian Thrun in 2010 after having to have closed MKD due to the housing crisis in 2009. Astro and Sebastian had recently co-founded Google X (how it was known at the time, now it is just “X”) along with Sergey Brin and they were looking at many of the world’s biggest problems. Affordable healthy, durable housing was one of the problems they were exploring. Given my passions and experiences, this was right up my alley! So, I joined them in late 2010.
MoL: What is X and what did you do there? What is their mission?
MK: X is the “moonshot factory” within Alphabet. They work on creating radical new technologies to solve some of the world’s hardest problems. X is a diverse group of inventors and entrepreneurs who build and launch technologies that aim to improve the lives of millions, even billions, of people. The goal of teams at X is to create a 10x positive impact on the world’s most intractable problems, not just a 10% improvement. They approach projects that have the aspiration and riskiness of research with the speed and ambition of a startup.
While I was at X I worked with a group of software engineers and designers and we looked at possible solutions for making healthy, durable, sustainable buildings affordable for everyone using generative software. X is run by Astro Teller, an incredible leader, inventor, mentor and dear friend. I feel fortunate to still be working with folks on Astro’s team on some of our current Future Workplace innovations.
Bay View at Charleston East at Google – photo courtesy of Iwan Baan
MoL: You co-founded Flux while at X. What does this company do and how is it helping sustainable architects?
MK: Yes, some of us who were working at X on the problem of scalable affordable sustainable buildings co-founded a spin-out from X, a small start-up company called Flux. We worked on a number of highly ambitious endeavors that ultimately were successful in functionality but not in scalability as they were ahead of the time and industry. I am hopeful that some of these ideas are now becoming reality around the AEC world.
MoL: What is Google R+D Lab for the Built Environment? Can you tell us more about your work as the director of the lab?
MK: Yes! We originally set up the R&D lab in 2015 when we started working on our first ground-up projects. Up to that point, we had only been doing tenant improvements in existing buildings. Google’s leadership wanted to take the opportunity to really push the envelope of what is possible and try to achieve the company’s north star ambitious aspirations. Some of those aspirations include studying how we could design and construct buildings that don’t create any carbon, that produce their own energy, that is net positive water, that can be really healthy for people, that can be highly adaptable for decades to come, and be scalable to millions. This is, of course, challenging to do because to be scalable it needs to be cost-effective and cost no more than traditional buildings, and not take any more time, and not have any more risk. That is nearly an impossible problem, especially for individual single buildings to tackle alone. However, if we look across our portfolio and pipeline of multiple buildings and campuses, we have a shot.
We set up the R&D lab as a way to both study what might be possible, with a lot of trial and error, to see if we can utilize the scale of our entire portfolio instead of just one project as a way to move from what is on the market today (lower left corner of a graph) to our north star aspirations (upper right corner of a graph). Can we help to move all of our projects up higher along that trajectory? That’s really why we set up the R&D lab, to try to help move us along in ways that single projects could not, where we can do research and development in advance of a project starting.,. For example, are there ways that we could cover our entire buildings with solar panels that are beautiful, efficient and have a meaningful return on investment? And if that doesn’t exist on the market yet, how do we do this?
The kind of research and testing required for materials and products that are not yet on the market – but could possibly be solid solutions in the future – is a near impossibility for an individual project to do while also hitting their budget and schedule. Our R+D group strives to do that work in advance for initiatives that seem promising for solving our toughest problems and highest priorities. We research and talk to all sorts of people and look at all sorts of companies and see what products they might be developing that are not on the market yet. If there is a promising solution that we test is working and produces the results we are striving for, is there a way to help bring that to market sooner?
In a nutshell, that’s really why we have the R&D lab, to try to help move toward our lofty north star aspirations. As we come up with some of those solutions and we’ve tested them, then we can start to offer them to Google individual projects. And some of those things only make sense when you have the scale across our projects. You can only get the price point where they can be scalable when we do it on ten buildings versus just one.
Google Bay View
MoL: What is sustainable design? Can sustainable design be accessible to anyone?
MK: Sustainable design seeks to reduce negative impacts on the environment, and the health and comfort of building occupants, thereby improving building performance. The basic objectives of sustainability are to reduce consumption of non-renewable resources, minimize waste, and create healthy, productive environments. How one approaches that for each project can vary widely based on context, program, climate conditions and priorities.
For some projects it might be more about creating super healthy spaces inside (so non-off gassing finishes and furniture plus high-quality air filtration systems), for others, it might be more about energy or water or carbon. Luckily there are increasingly more products and systems on the market and as the demand and supply both rise, the cost lowers. This is luckily true for both housing as well as commercial buildings. I had the great honor to work on the Bay View and Charleston East first ground-up projects for Google. They are the largest projects to receive Living Building Challenge certification and Bay View was recently awarded as the largest LEED Platinum building in the world by the USGBC. They were designed in collaboration with BIG Architects, Heatherwick Studio, and Adamson Architects (plus many more incredible engineers and builders) to be net-water-positive, healthy and hopefully vibrant and functional for generations to come. We wanted to share all of our learnings from the projects with others with the goal of making the solutions more scalable and accessible to everyone, so there is a ton of info at:
MoL: How do you integrate the natural environment into your designs? Is this important, and if so, why?
MK: There are a number of approaches to this. One is Biophilic design, which is a concept used within the building industry to increase occupant connectivity to the natural environment through the use of direct nature, indirect nature, and space and place conditions. This is work that Google’s real estate group has been heavily invested in and key drivers for our workplace design. I find this paper from Terrapin to be helpful when looking at how best to incorporate the best of Biophilic design: 14 Patterns of Biophilic design. Another is learning from nature, something called Biomimicry, which is a nature-inspired design that leverages learnings from sustainable systems and patterns found in trees, water systems, roots, plants, animals that can be applied to how we design, build and even grow buildings. Another approach can simply be using natural materials, bringing nature in, and maximizing the connection to the outdoors with views and natural light.
MoL: What advice can you give to the next generation of green architects?
MK: Do whatever you can to surround yourself with people who share your values, and whom you enjoy working with and learning from and making with. If there is anything to learn from my journey so far is that any successes I have is only in collaboration with and because of the extraordinary people, I have been so lucky to spend my days with. Working on ambitious designs can be tough, so I hope you can surround yourself with people you enjoy and are able to find joy each day in the process as well as the end product.
FILM
Photography courtesy of Michelle Kaufmann
Steven Peck is dedicated to creating greener, healthier & resilient cities with nature & urban agriculture.
Arno Adkins is Partner at COOKFOX, an architectural studio dedicated to integrated, environmentally responsive design.
From private villas to hotels to treehouses, Peter Pichler has established a global sustainable impact with his architectural laboratory, spanning Europe, the United States, and the United Arab Emirates.