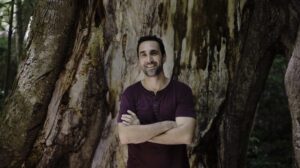
Masaya Co — Sustainable Furniture from Seed to Seat
MasayaCo is a sustainable furniture company on a mission to combat climate change through reforestation & sustainable design.
USA
Marisa Albanese May 21, 2021
Founded in 1944, the furniture brand Emeco has pioneered a myriad of sustainable products including its signature aluminum chairs. Handmade with recycled aluminum, Emeco’s chairs have stood the test of time not only due to their durable structure but also due to their impeccable design. As reflected through their functional yet elegant aesthetic, Emeco perfectly balances innovation as well as material development, integrating sustainability and longevity throughout every step of their design process.
Since taking the helm from his father, Gregg Buchbinder has led Emeco into a new era as the company’s CEO, reinventing the brand’s classic chair design through various collaborations with influential contemporary architects, such as Phillip Stark and Frank Gehry. Despite shifting the company’s focus from utilitarian to modern, architectural furniture, Buchbinder still admires and prioritizes the extensive craftsmanship involved in creating Emeco’s chairs, a 77-step process that merges 80% recycled aluminum and artistic precision.
With an eye toward our planet’s future, Emeco strives to reduce its environmental impact as much as possible, challenging themselves with higher sustainability goals each year. Whether it be measuring the carbon footprint of each chair produced or seeking out new alternatives for material upcycling, Emeco is constantly refining its vision of sustainability, durability, and artistry.
Mood of Living: Where did you grow up?
Gregg Buchbinder: Huntington Beach, California.
Gregg Buchbinder
MoL: Where did you go to school and what did you study?
GB: Marina High School – surf team. University of Southern California – didn’t study much, mostly surfed and sailed.
MoL: How did your childhood and parent’s professions influence your career and life?
GB: My mom was an artist and designer. She always had some kind of art project going on. She especially loved to paint and do the interiors of homes. My dad was an engineer who was always making or fixing things. He did some furniture projects for Herman Miller. Our mid-century modern home was filled with reject (now called prototype) chairs.
MoL: What was your first job?
GB: My first real job was working for my dad. He had a bunch of workshops and I learned all the trades – metalworking, woodworking, fiberglass (great for surfboards), and upholstery.
MoL: When did Emeco collaborate with the Navy to create the 1006 Navy Chair? Why did the government assign Alcoa experts and founder Wilton C. Dinges to design and build these chairs?
GB: The Navy had many constraints for the chair they needed for their ships. It had to be non-corrosive to hold up to the salt air, fire proof for safety on ships, non-magnetic to keep from interfering with the navigation, lightweight to keep the ships from being top heavy, and super strong so the big burly sailors could not destroy them while out at sea. Emeco collaborated with ALOCA to use the right alloy of aluminum which was best for the unique 77 Step process they developed to make the Navy Chair. Some of the steps in the process included cutting, forming, welding, grinding, annealing, heat treating, hand finishing, and anodizing.
MoL: What were the unique specifications to create this chair? How was sustainability incorporated into the brand at the time?
GB: At the time in 1944 sustainability had not been conceived. During the war there was a shortage of raw materials and Americans scrap drives to contribute to the war effort.
The Factory
MoL: When and why did your father buy Emeco? What was the state of the company when he bought it? What Inspired you to buy the company in 1998 and what was your vision?
GB: My father was making metal understructures for fixed chairs and tables for the mess halls of Navy ships. These metal understructures were welded down to the deck of the ships so the furniture would stay in place and not slide around as the ships would roll in heavy seas. The shipbuilder my father was working for told him about Emeco. At the time Emeco was going out of business and the shipbuilder needed Emeco’s extraordinary Navy chairs for their ships. I always admired the Navy chair. When I saw the craftsmanship and steps in the process using 80% recycled aluminum to make a chair that was tested to last 150 years, I realized it was the best chair ever made. My vision was to expand our sales focusing on architects and designers.
MoL: Is your factory still in the original location? How important is it to you to have strong relationships with your community? How do you maintain compassion for your employees while still growing your business?
GB: Emeco is still located in Hanover, Pennsylvania. In addition to having the majority of our workforce living in the community, we also source the majority of supplies and materials for manufacturing locally.
MoL: What is your 77-step process and how are you able to achieve a stronger form of aluminum?
GB: The 77-Step process was developed by Emeco. We start the process using soft aluminum which allows us to effortlessly form seat bottoms and bend aluminum extrusions smoothly. Emeco’s secret to the aluminum’s strength comes down to chemistry. Pure aluminum is combined with other elements to create a high-strength alloy. Common elements used to increase the strength and formability of aluminum include silicon, magnesium and copper. Emeco further strengthens the aluminum chairs by heat-treating followed by rapid cooling. This process freezes the atoms in place strengthening the aluminum. Finally the chairs are placed in an aging oven overnight to achieve maximum hardness. This process inhibits the movement of atoms relative to each other, which makes for a super strong chair.
MoL: Sustainable practices and a commitment to minimize its impact on the environment is at the core of your brand mission. What SDG goals do you currently implement and what goals do you aim to pursue in the future?
GB: At Emeco we always try to tread lightly on the planet in all areas of our company. Our internal product team does ongoing engineering, research, and development for sustainability and longevity of materials – Life cycle analysis, life extension opportunities (repair), and end of life issues (recycling).
Now that we are measuring our carbon foot print on every chair we make, it’s much easier to set realistic and achievable SDG goals. We now know that energy use at our factory causes the most carbon emissions. One of our SDG goals is to use clean renewable energy. Another SDG goal for each chair we make is longevity. This requires working with specialists like material scientist to aid in up-cycling waste material and engineers to create the proper tools and processes for responsible production.
MoL: Each of your products comes with a declaration of its unique C02 emission. Do you believe consumers are making educated choices on purchases based on sustainability? Do you believe the future consumer will care more than they do now?
GB: For products, consumers should know longevity (i.e.; warranty) and the actual carbon footprint. The more manufacturers provide this information, the more specifiers and regular consumers will be able to know what to ask for. The more that consumers ask, the more manufacturers will include this information. We think it is very important to normalize this disclosure of carbon footprint. We are at a point in climate change where we are seeing devastating effects around the globe, it’s on all of us to reduce our carbon footprint. As a small company with good intentions, we’ve often found ourselves limited when wanting to measure and determine our impact. By measuring our carbon footprint we can educate ourselves and consumers to help promote a kind of environmentalism that can be accessed by all. By enabling measurement and transparency, we not only encourage consumers to research what they buy, but inspire all responsible companies to measure, improve and ultimately reduce emissions.
MoL: Emeco has collaborated with many iconic designers and brands over the years. What is the criteria for you to choose to work with a designer or brand? What is unique about the 1006 Navy Chair that has had so much influence over modern design
GB: We don’t have a formal process or a criteria list for the architects or designers we choose to collaborate. And we don’t use focus groups to determine the products or attributes to make. The path we follow is based on our mission of doing the least amount of impact to the planet. It’s easy for us to make decisions, we just stick to our mission.
I believe the reason the 1006 Navy Chair has had so much influence over modern design due to it’s iconic status. This status is based upon a utilitarian product made for a purpose, like a pair of Levi’s or a Jeep. In addition, it sets a high bar on using waste and creating an extra ordinary long life.
MoL: With the launch of the ‘On and On chair’ this year, designed by Barber & Osgerby, you have created a piece of furniture that can be recycled over and over again. Do you see Emeco working towards more circular products in the future?
GB: Creating a circular for all products we make is Emeco’s goal. It takes a long time and is difficult to achieve. The On & On chair design took 3 years to develop, however the recycled PET material that can be endlessly recycled without any degradation in the material properties took 13 years.
MoL: When did you collaborate with the iconic designer Phillip Stark, and how did this partnership impact your business?
GB: Starck took the DNA of our utilitarian chair for Navy ships and made it sexy. Overnight Emeco was transformed from an industrial chair company to a design furniture company.
MoL: How did you begin your partnership with Mr. Gehyr in the creation of a new chair, and what makes this chair unique?
GB: Our collaboration with Frank Gehry began when I went to his studio to see how he was using the 120 Emeco Hudson swivel chairs he purchased. Frank asked me to critique another chair he designed. He liked my critique and said “Lets make a chair”.
MoL: Your internal product team does ongoing engineering, research, and development for sustainability and longevity of materials. What are the core areas that they work on?
GB: The core area of their work is in the use of sustainable materials, life cycle analysis, end of life issues (recycling) and very active in measuring our carbon footprint of every chair we make.
Za by Naoto Fukasawa
MoL: Tell us about your collaboration with Coca Cola. How are you “up-cycling” plastic Coca Cola bottles from landfills to make a scratch-resistant chair for heavy-duty use? What is the process of recycling plastic?
GB: Today there are a number of sources to obtain material made from recycled plastic bottles. There are companies who get there material from third world countries who do not have any recycling facilities. We decided to get our material from reclamation centers in the US for several reasons. First, it does not have to be transported half way around the world; second, since there is an over abundance of waste in the US since China stopped taking our waste; finally, we support local business so they can grow and help other companies with their waste material needs.
MoL: What advice can you give to the next generation of people interested in creating company with a mission to do good for the world?
GB: Find a mission you really believe in. Stick to your mission in every decision you have to make. Your decisions will be easy.
Photography courtesy of EMECO
MasayaCo is a sustainable furniture company on a mission to combat climate change through reforestation & sustainable design.
Founder Treana Peake, supports artisan partnerships and funds development work through the Obakki Foundation.
ÁBBATTE creates handmade textiles in Spain on the grounds of a 13th -century Cistercian monastery in the town of Segovia.